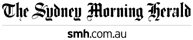
Name: Philippe Vincent
The profession: Sewing for space
The organisation: Space Machines Company
The title: Industrial sewing machinist
The pay: Between $50 - $300 per hour (based on a range of factors including complexity, design requirements and scale).
Usually, industrial sewing machinist Philippe Vincent works on umbrellas or violin bags, until he was asked to sew space material.Credit: Hugo Munoz
10am: My day starts by turning on about twenty different light switches in the co-op building where I work. It’s called Tortuga Studios, and it’s filled with other people who are self-employed doing things like photography or set design. We’re all friends.
I often receive enquiries via my website for different or niche projects. I might be sewing a custom bag for a violin or sewing synthetic grass or carpet for a product for a furniture company. I usually have five to ten jobs going at the same time. Sometimes I’ll spend an hour or so first thing on email, but generally, it’s straight to it.
I started sewing when I was 13, making clothes for myself. It progressed into knitwear on industrial knitting machines and took off from there. Domestic sewing machines try to cram many features into the machine, but in industrial machines there’s one machine for each task. They are heavy, and set into a table, you can’t pick them up and walk around the room with them.
11am: In industrial design there is often no pattern to follow, so I’ll make one. Today I’m doing a valance for a high-end umbrella for a regular client. When Space Machines Company reached out needing someone to sew multi-layer insulation in Australia’s largest-ever private satellite, I had to create patterns and mock-up versions for each blanket.
Loading
Before I began, I had zero knowledge of the space industry or satellites. It was so interesting to learn about. Multi-layer insulation is a thermal insulation composed of multiple layers of thin sheets and is often used on spacecraft.
It’s primarily intended to reduce heat loss by thermal radiation, and withstand the extreme temperatures of space. It can be easily penetrated by high-speed debris, so each blanket had to go through multiple rounds of tests to make sure it was sturdy enough ahead of the launch.
1pm: A client comes into the studio to check a prototype. Normally, I work from here, but for the multi-layer insulation project I went to the Space Machine Company’s site where the satellite was being built because it needed to be done in a sterile environment.